Galling in Stainless Steel
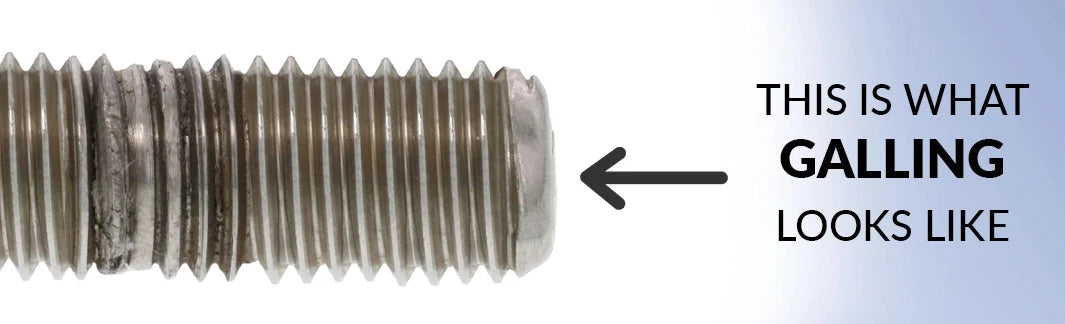
Galling and How to Prevent It
It won’t budge. Is it defective?
You’re tightening a stainless steel bolt in a rigging assembly and all of a sudden … nothing. The bolt won’t go in any more. Worse, it seems fused in place, and you can’t even back the bolt out. What happened to your rigging fittings here?
What is “galling?”
In this case, it’s likely you’ve encountered what’s called “galling.”
Galling is a type of welding caused by the heat and friction produced between two sliding forces, like between the threads of a bolt, nut, or tapped hole. Galling is common while working with fasteners and turnbuckles where threads rub against each other more and more as they are tightened.
The tightening pressure causes the threads’ coating to chip and break into small metal filings. The increased heat and friction can then weld these small filings between the threads, creating a strong but undesirable bond between hardware pieces. The process can happen almost instantly.
Galling can result in an expensive, welded mess that cannot be taken apart. Generally, the fasteners must be split or cut in order to dismantle the rigging.
Are some fasteners more prone to galling than others?
Stainless steel, aluminum, and titanium are most susceptible to galling. Even hot-dipped galvanized fittings are very susceptible, despite their protective anti-rust features.
These materials all have thin oxide coatings that protect against everyday friction and wear, but the intense heat created when adjusting threaded fasteners under load can break these coatings down.
Locknuts are especially prone to galling because they are specifically designed to produce high friction with mating threads to prevent loosening over time.
How can you avoid galling?
Since heat and friction are the two main ingredients in an undesirable galling situation, you can reduce the risk by following some simple tips to reduce both of them. Here are four ways to prevent metal galling in your rigging assemblies:
- Reduce installation speeds.
- Reduce Tension on Components.
- Be mindful of environmental conditions.
- Do not over-torque your components.
- Use Larger Threaded Fittings.
- Apply thread lubricant before installation.
Galling occurs most commonly when using high-speed drivers since their power can produce heat and friction much faster than a human with a manual tool. Since power tools do not need to adjust their grip, the friction and heat is continuous on the workpiece. Avoid high-power tools when installing stainless, aluminum, and titanium fasteners. Tools with slower installation speeds will greatly reduce friction and lower your risk of galling the threads.
Tension in load holding assemblies containing threaded rigging fittings such as turnbuckles and eyebolts especially prone to galling. Galling can occur even when relieving tension in an assembly. We recommend using cable grips in conjunction with cable pullers, or hoists to safely relieve the tension on the turnbuckle or eyebolt before making major adjustments in take-up or threaded length. Minor adjustments can be made under load, but higher tension, higher speed of adjustment, and longer lengths of adjustment increase the likelihood of galling.
Examine the threads of your workpieces for wear or dirt, since both can create unnecessary friction while tightening. Also remember that although galling mostly occurs during tightening and installation, thermal conditions can contribute to the breakdown of protective metal coatings. Before installation, store your fasteners and tools out of direct sunlight and away from heat sources to reduce the risk of a costly galling incident.
Over-torquing a nut, bolt, or turnbuckle can damage the threads through sheer physical pressure, increasing the risk of galling and bonding. Know the torque requirements for all of your components before you begin and stick to the guidelines recommended by their manufacturer.
Using larger threaded fittings will reduce the likelihood of galling. Galling is caused by pressure between two threaded surfaces. The pressure is determined by the load on the fittings, and the surface area of the engaged threads. In most circumstances, rigging components are matched and selected based on their working load limit in relation to the application. If galling continues to occur, or is suspected to occur for your application, sone solution could be to increase the size of the threaded fittings. Doing so will reduce the pressure on the threads by increasing the engaged surface area of the threads.
Use an anti-galling or never-seize lubricant to reduce friction in threaded fasteners. These compounds are specifically designed to reduce galling without sacrificing the strength of your rigging setup. Stay away from spray lubricants and nickel-based anti-seize. Ideally, always use metal-free anti-seize in corrosive environments because dissimilar metals in contact with each other can cause galvanic corrosion. We’ve found that LOCTITE LB 8070 is a suitable choice for most applications.