General Warnings and Instructions
READ ALL WARNINGS BEFORE USING THIS PUBLICATION. FAILURE TO FOLLOW WARNINGS AND INSTRUCTIONS MAY RESULTS IN SERIOUS INJURY OR DEATH.
General Use Statement
E-Rigging.com assumes no responsibility for the use or misapplication of any product sold by this firm. Responsibility for design and use decisions rests with the user. All products are sold with the express understanding that the purchaser is thoroughly familiar with the correct application and safe use of same. Use all products properly, in a safe manner and for the application for which they are intended. It would be impossible in the scope of this publication to list all possible dangers and misapplications associated with the use of all products contained herein. However, to promote safe rigging habits, the most common safety topics and hazards associated with the use of these products are listed in the publication below.
Key Safety Considerations
- Never exceed the Working Load Limit (WLL).
- Match components properly.
- Keep out from under a raised load.
- Avoid shock loads.
- Inspect products regularly.
- Read product Instructions before use.
Units of Measure
- Load Ratings are stated in short tons (2,000 lbs.) or pounds unless otherwise specified.
- All dimensions are in inches or feet unless stated otherwise.
- All weights and dimensions are approximate and are subject to change.
Breaking Strength / Ultimate Strength
Breaking Strength is the typical force at which a newly manufactured product will fail under controlled loading conditions. The Breaking Strength is calculated by using a tensile testing machine to apply a constantly increasing in-line force at a uniform rate on a product until it fails. Breaking Load, Minimum Breaking Strength (MBS), and Minimum Breaking Load (MBL) are terms also used to represent Breaking Strength.
Breaking Strengths, when published, are obtained under controlled laboratory conditions. Listing the Breaking Strength does not mean the Working Load Limit should ever be exceeded. Refer to the Working Load Limit for service or design purposes.
Design Factor
An industry term usually computed by dividing the catalog Breaking Strength by the catalog Working Load Limit and generally expressed as a ratio. For example: 5 to 1, or 5:1 would mean the item has a breaking strength 5 times more than the working load limit. Expressed in real units: 10 ton breaking load, and 2 ton working load limit. The purpose of the design factor is ensure:
- A product has adequate fatigue life under repetitive loading
- The product can endure unexpected loading conditions with a margin of error without immediate failure.
- The product can still maintain the rated capacity even with wear and degradation within the acceptable limits before failing inspection.
Working Load Limit / Rated Load
The Working Load Limit is the maximum uniform in-line load which should ever be applied to the product. All load ratings are based upon usual environmental conditions and consideration must be given to unusual conditions such as extreme high or low temperatures, chemical solutions or vapors, prolonged immersion in salt water, etc. Such conditions or high-risk applications may necessitate reducing the Working Load Limit. Avoid side loading as many fittings are not rated for side load applications. Side loading on side-load rated products will have special directions for reduction of WLL when side loaded.
NEVER EXCEED THE WORKING LOAD LIMIT
Working Load Limit is the term used throughout E-Rigging.com. There are, however, other terms used in the industry which are interchangeable with the term Working Load Limit. These are: WLL, SWL, Safe Working Load, Rated Load Value, Resulting Safe Working Load, Rated Load and Rated Capacity.
Proof Test Load
The term "Proof Test" designates a quality control test applied to the product for the sole purpose of detecting defects in material or manufacture. The Proof Test Load (usually twice the Working Load Limit) is the load which the product withstood without deformation when new and under laboratory test conditions. A constantly increasing force is applied in direct line to the product at a uniform rate of speed on a standard tensile testing machine. The “proof test load” is often called “proof load”, or “proof”.
The Proof Load rating does not mean the Working Load Limit should ever be exceeded.
Termination Efficiency
Termination Efficiency is the percentage of strength a rigging assembly retains by applying an end termination to wire rope, cable, rope, chain, etc. For example: When applying swage sleeves to wire rope, the Working Load Limit of the assembly will be 90% as strong as the wire rope’s working load limit. End terminations that have termination efficiency considerations will have the termination efficiency ratings listed on the product page.
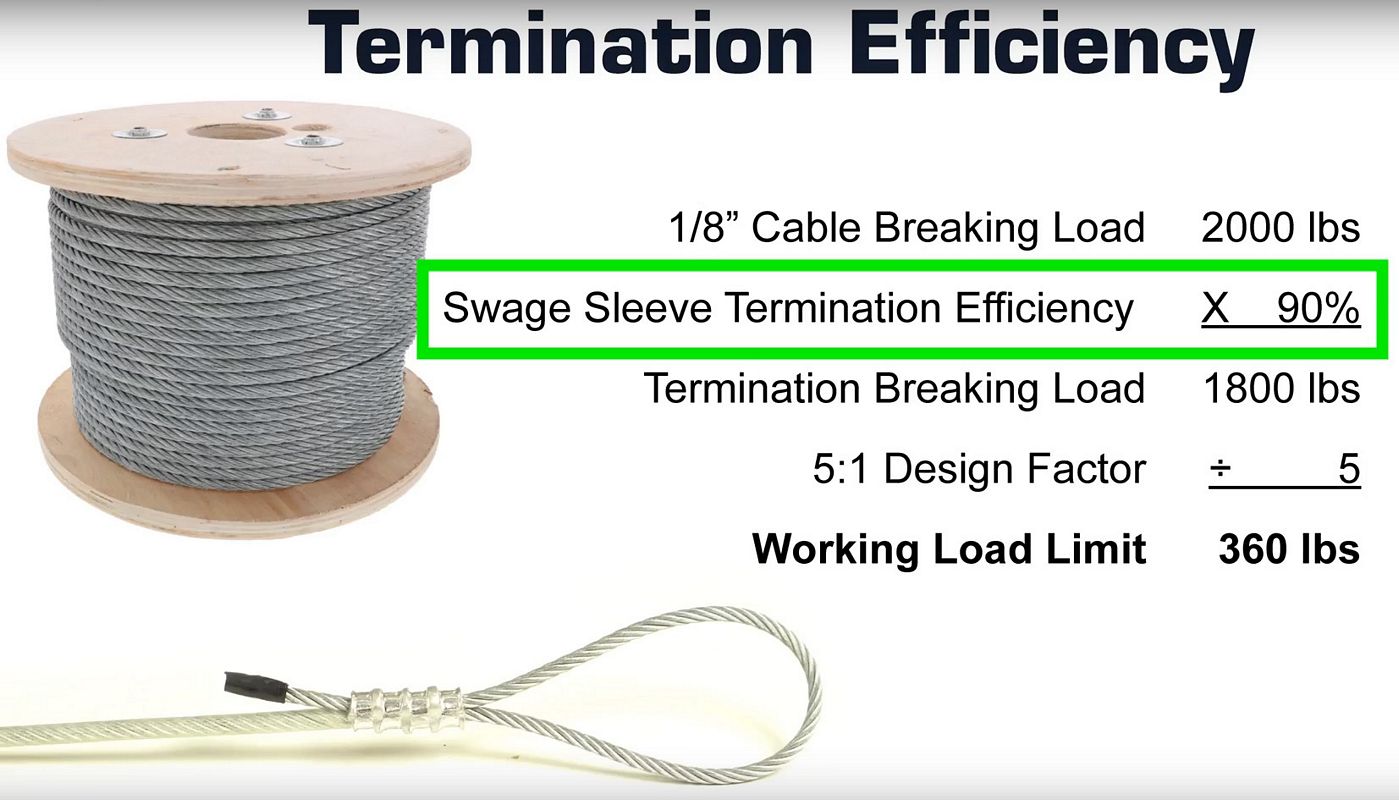
Typical Product Termination Efficiencies
- Buttons: 30-60%: Termination efficiency for buttons depends on size, and swaging equipment. Testing is required before use in critical applications.
- Aluminum and Copper Sleeves: 90%
- Wire Rope Clips: 80-90%: Malleable cast iron clips should only be used in non-critical applications. ASME, OSHA, and ASTM recommend only forged clips for critical applications.
Shock Load
A load resulting from rapid change of movement, such as impacting, jerking or swinging of a static load is referred to as shock load. Sudden release of tension is another form of shock loading. Shock loads are generally significantly greater than static loads. Any shock loading must be considered when selecting the item for use in a system. Such breaks can cause loads to fail or swing out of control, possibly resulting in serious injury or death as well as major property damage.
Remember: Any Product will break if abused, misused, overused, or not maintained properly. Avoid shock loads as they may exceed the Working Load Limit.
Raised Load
Keep out from under a raised load, do not operate a load over people, and do not ride on loads. Take notice of the recommendation from the National Safety Council Accident Prevention Manual concerning all lifting operations: "All employees working on cranes or hoists or assisting in hooking or arranging a load should be instructed to keep out from under the load. From a safety standpoint, one factor is paramount: Conduct all lifting operations in such a manner that if there were an equipment failure, no personnel would be injured. This means keep out from under a raised load and keep out of line of force of any load."
Properly Matching Components
Make certain that components such as hooks, links, turnbuckles, shackles, etc. used with wire rope (or chain or cordage) are of suitable material size and strength to provide adequate safety protection. Attachments must be properly installed and must have a Working Load Limit at least equal to the product with which they are used. The rigging assembly can only be rated up to the weakest component minus any termination efficiencies.
Remember: Just as “Any chain is only as strong as its weakest link”, any rigging assembly is only as strong as its weakest component.
Modifications and Welding affect the Working Load Limit
Working Load Limit will not apply if product has been welded or otherwise modified. It should also be noted that it is the ultimate responsibility of the end user to determine a Working Load Limit for each application.
Regular Inspections
- Inspect products regularly for visible damage, cracks, wear, elongation, rust, etc. Protect all products from corrosion. The need for periodic inspections cannot be overemphasized. No product can keep operating at its rated capacity indefinitely. Periodic inspections help determine when to replace a product and reduce rigging hazards. Keep inspection records to help pinpoint problems and to ensure periodic inspection intervals.
- Due to the diversity of the products and uses to which they can be put, it would be counterproductive to make blanket recommendations for inspection procedures and frequency. The best results will be achieved when qualified personnel base their decisions on information from rigging and engineering manuals and on experience from actual use in the field.
- Frequency of inspection will depend on environmental conditions, application, storage or product prior to use, frequency of use, etc. When in doubt, inspect products prior to each use. Carefully check each item for wear, deformation, cracks or elongation - a sure sign of imminent failure. Immediately withdraw such items from service.
- Rust damage is another potential hazard. When in doubt about the extent of corrosion or other damage, withdraw the items from service.
- Destroy, rather than discard, items that have been judged defective. They might be used again by someone not aware of the hazard involved.
- Click here to read more about materials and finishes to combat corrosion with our instructional video and text guide.
- Click here to learn more about Stainless Steel corrosion resistance and its features and limitations with our informative text guide.
Product Specific Instructions
It is important to read and understand product specific instructions that are displayed on the product pages, and/or supplied with the products.Polyester web slings, Roundslings, Wire rope clips, Swivel Hoist rings, eyebolts, and hoisting equipment are examples of products that have additional instructions, but be sure to check each product for published instructions be fore use.
Countries of Origin
We travel across the world visiting countries and factories to qualify and inspect facilities to ensure the products we offer are high quality and suitable for their intended applications. As a matter of policy, we are trying to make as many of the products we sell ourselves and have invested about $3 million dollars in machining and testing equipment over the last 3 years to help us achieve this objective. The tariffs and increasing political tensions between the U.S. and China have us moving to suppliers in other countries as much as is practical. For Items marked as imported, the cable we stock comes from Thailand and South Korea. Forgings come from China. Stainless parts come from Thailand. Chain products come from China. We also are adding more domestically produced products to our website and will try to offer them at the most competitive prices we can.
Fraction/Decimal/Metric Length Conversions
Fraction | Decimal | Metric |
---|---|---|
1/64 | 0.015625 | 0.397 mm |
1/32 | 0.031250 | 0.794 mm |
3/64 | 0.046880 | 1.191 mm |
1/16 | 0.062500 | 1.588 mm |
5/64 | 0.078130 | 1.985 mm |
3/32 | 0.093750 | 2.381 mm |
7/64 | 0.109380 | 2.778 mm |
1/8 | 0.125000 | 3.175 mm |
9/64 | 0.140630 | 3.572 mm |
5/32 | 0.156250 | 3.969 mm |
3/16 | 0.187500 | 4.763 mm |
7/32 | 0.218750 | 5.556 mm |
Fraction | Decimal | Metric |
---|---|---|
1/4 | 0.250000 | 6.350 mm |
9/32 | 0.281250 | 7.144 mm |
5/16 | 0.312500 | 7.938 mm |
3/8 | 0.375000 | 9.525 mm |
7/16 | 0.437500 | 11.113 mm |
1/2 | 0.500000 | 12.700 mm |
9/16 | 0.562500 | 14.288 mm |
5/8 | 0.625000 | 15.875 mm |
11/16 | 0.687500 | 17.463 mm |
3/4 | 0.750000 | 19.050 mm |
7/8 | 0.875000 | 22.225 mm |
1 | 1.000000 | 25.400 mm |
Wire Rope & Cable Warnings and Instructions
Wire rope is a machine, like any machine, it needs proper care and maintenance for optimal safety and long service life. Please read our Rope & Cable Warnings and Instructions for more specific and detailed information.
Key Points:
- Never exceed the rated capacity.
- Use attachments that match the wire rope’s rated capacity.
- Avoid shock loads.
- Destroy, rather than discard, wire rope to be retired
- Inspect wire rope regularly.
Polyester Web Sling Warnings and Instructions
Polyester Web Slings are versatile tools, but you must learn and understand their limitations, operating instructions, and environmental considerations prior to use. Click here to read our full Polyester Web Sling Warnings and Instructions Guide.
Disclaimer of Warranties and Limitation of Liability
Seller warrants that its goods are free from defects in materials and workmanship. Accordingly, Seller’s liability is limited to replacing without charge or refunding the purchase price, or making fair allowance for any noncompliance with any specifications or any defects in materials or workmanship in its products existing at the time of delivery. Seller requires written notice and the return of the product to establish any claim. SELLER MAKES NO OTHER WARRANTY OF ANY KIND WHATEVER, EXPRESS OR IMPLIED, AND ALL IMPLIED WARRANTIES OR MERCHANTABILITY OR FITNESS FOR A PARTICULAR PURPOSE WHICH EXCEED THE ABOVE OBLIGATION ARE HEREBY DISCLAIMED BY SELLER AND EXCLUDED. Seller will not be liable for any consequential damages, loss or expense arising in connection with the use or inability whatever, regardless of whether damage, loss, or expense results from any act or failure to act by Seller, whether negligent or willful, or from any other reason. Unless specifically stated, products are of commercial quality and standards. Buyer must determine suitability for the products particular use or purpose and will assume any and all risk and liability whatsoever resulting from the use of all products, whether used singly or in combination with other products or components. If requested and/or applicable, manufacturer's material certifications may be provided with no representations made as to their accuracy.